Glossary
Navigate the complex world of product costing, cost engineering, and carbon management with our comprehensive glossary. Understand essential industry terms and find relevant resources to deepen your knowledge.
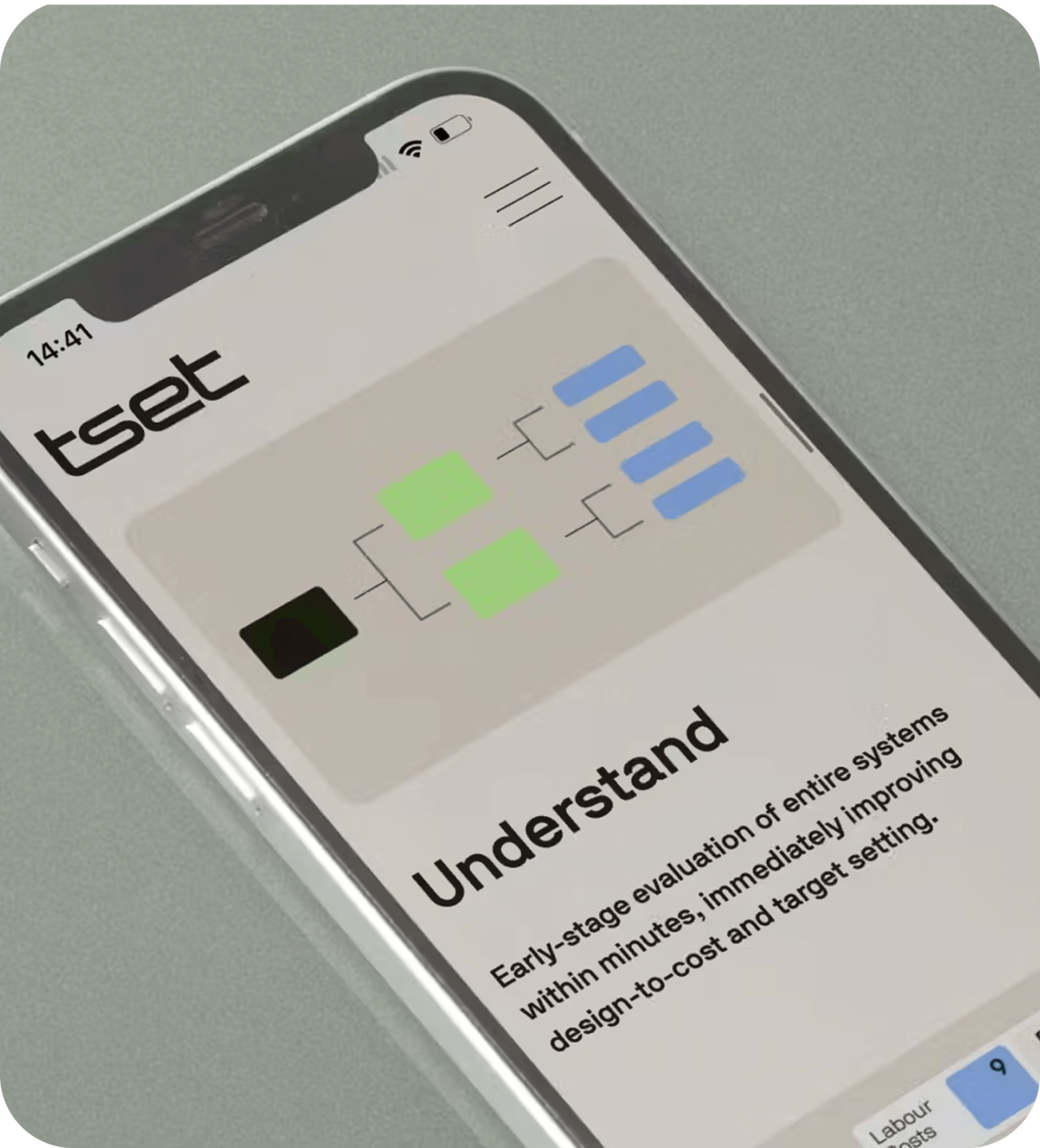
Our glossary offers clear and concise explanations of essential keywords and terms related to product costing, cost engineering, and carbon management. Whether you are a cost engineer, procurement professional, R&D engineer, or manufacturing decision-maker, this resource will assist you in navigating industry-specific concepts and finding educational resources.
A–C
CBAM (Carbon Border Adjustment Mechanism)
An EU regulation that imposes a carbon tariff on imported goods to encourage manufacturers to reduce emissions and adopt more sustainable practices.
CBD (Cost-Break-Down)
A detailed analysis of a product’s total cost, segmented into key components, to improve transparency and cost efficiency. It is essential for cost engineering, supplier negotiations, and manufacturing cost optimization.
Carbon Management Software
A digital solution that helps companies measure, track, and reduce their carbon footprint across the supply chain.
Cost Analysis
A systematic evaluation of costs associated with a product, service, or process to identify inefficiencies and savings potential.
Cost and Value Engineering
A methodology that balances cost efficiency and product value to enhance profitability.
Cost Calculation Tool
A software application used to estimate and calculate the costs of manufacturing products or providing services.
Cost Driver
A factor that significantly influences the total cost of a product or process, such as raw material prices, labor, or energy consumption.
Cost Engineering
A discipline focused on cost control, cost optimization, and cost estimation in product development and manufacturing.
Cost Estimation
Software designed to calculate and estimate production costs by analyzing materials, labor, and manufacturing processes.
Cost Management Software
A tool that enables businesses to monitor, control, and optimize costs across projects, procurement, and production.
Cost Model
A structured representation of all cost components in manufacturing, helping businesses forecast and optimize costs.
Cost Optimization
The process of reducing expenses while maintaining operational efficiency and product quality.
D–E
Design-to-Cost
An approach where cost targets are set during the design phase to ensure profitability while meeting product requirements.
Design-to-CO₂
A sustainability-driven methodology where products are designed with minimal carbon impact in mind.
Design-to-Sustainability
An approach that integrates sustainability principles into product development to reduce environmental impact.
Emission Reporting
A regulatory process where companies document and disclose their greenhouse gas emissions, often for compliance with environmental laws.
Estimating and Costing
The process of predicting the expenses involved in manufacturing a product to support budgeting and pricing decisions.
F–H
Forging
A metalworking process that shapes material using compressive forces, typically by hammering or pressing, enhancing the strength and durability of the final product.
High Pressure Die Casting
A manufacturing method where molten metal is forced into a steel mold under high pressure, producing parts with precise dimensions and smooth surfaces.
I–L
Injection Molding
A manufacturing technique where molten material, usually plastic, is injected into a mold cavity under high pressure to form complex shapes with high precision and repeatability.
K–M
Machining
A manufacturing process involving the removal of material from a workpiece to achieve a desired shape and size, typically using tools like lathes, milling machines, and drills.
Make-or-Buy Cost Analysis
A financial assessment to decide whether a company should produce components in-house or outsource them.
Manufacturing Cost
The total expense of producing a product, covering raw materials, labor, and factory overhead costs.
Manufacturing Cost Management
A strategic approach to controlling production costs while maintaining product quality and efficiency.
Manufacturing Emissions
Greenhouse gas emissions resulting from industrial production processes, including energy use and raw material extraction.
Metal Stamping
A metal forming process where sheet metal is cut, shaped, and formed using dies and high-pressure presses, incorporating operations such as blanking, bending, punching, and deep drawing to produce precise, cost-effective components.
P–R
Predictive Costing
A data-driven approach to forecasting future product costs based on historical data, market trends, and cost models.
Procurement Costing
The process of calculating and managing costs associated with purchasing materials and components.
Product Carbon Footprint (PCF)
The total greenhouse gas emissions associated with a product's lifecycle, from raw material extraction to disposal.
Product Carbon Management
The process of measuring, reducing, and managing the carbon footprint of products throughout their lifecycle.
Product Cost Analysis
A systematic approach to evaluating the costs associated with a product, including raw materials, production, logistics, and indirect expenses.
Product Cost Benchmarking
A structured method for comparing product costs against competitors or industry standards to identify cost optimization opportunities.
Product Cost Calculation
The process of determining the total cost of producing a product, including materials, labor, overhead, and other expenses.
Product Cost Management (PCM)
A strategic approach to controlling and optimizing costs throughout the entire product lifecycle, from design to production.
Product Cost Management Software
A digital solution designed to analyze, optimize, and control product costs throughout the entire lifecycle.
Product Costing
The process of calculating the total cost of a product, considering materials, labor, manufacturing overhead, and logistics.
Product Costing Software / Product Cost Management Tool
A specialized tool used to calculate, manage, and optimize the costs of products throughout their lifecycle.
Product Manufacturing Costs
The total cost incurred in producing a product, including materials, labor, and overhead.
Product Cost Calculation
The process of estimating and analyzing the total cost of manufacturing a product.
Purchase Price Analysis
An evaluation of supplier pricing to ensure competitive and fair procurement costs.
Purchasing Costs
The total expenses incurred when acquiring goods and services for production.
S–T
Scope 3 Emissions
Indirect emissions in a company’s value chain, including supplier emissions, transportation, and product lifecycle impacts.
Scope 3 Upstream
The part of Scope 3 emissions related to supply chain activities, such as material extraction and supplier operations.
Sheet-Metal Forming
A fabrication process that shapes metal sheets into desired geometries using bending, stretching, or stamping techniques, commonly used for automotive and appliance parts.
Should Costing
A method used in procurement and cost engineering to estimate the fair price of a product or component based on its material, labor, and process costs.
Should Cost Analysis
A detailed breakdown of a product’s costs to determine its true value and enable more informed pricing and procurement decisions.
Should Cost Estimate
An estimation method used to predict the ideal cost of a product or component to support negotiation and cost transparency.
Sintering
A process that compacts and heats powdered materials below their melting point to form solid components with high strength and precision, often used in metal and ceramic manufacturing.
Supplier Negotiations
The process of discussing terms and prices with suppliers to achieve optimal cost savings and procurement efficiency.
Target Costing
A cost management approach where a product’s price is determined first, and the design is adjusted to meet cost objectives.
Transfer Die Stamping
A metal forming process where a workpiece is moved through multiple stations using a transfer system, enabling complex parts to be stamped and formed in a sequence of operations.
V–W
Value Analysis (VA)
A method to optimize product costs by analyzing the functions of a product and eliminating unnecessary expenses while maintaining quality.
Value Engineering (VE)
A structured process to enhance product value by improving functionality while reducing costs during the design and development phase.
Continue learning
Product Cost Benchmarking in Action
Cost benchmarking isn’t just about reducing expenses—it’s a strategic approach to improving product positioning, sourcing efficiency, and pricing decisions. This whitepaper provides a structured methodology to help manufacturers gain cost transparency, assess market competitiveness, and drive smarter business strategies.
Production Emissions in Technology Planning
Explore how manufacturers can systematically assess and reduce production-related CO₂ emissions in early product development.
Data-Driven Profit Optimization in Manufacturing
Learn how leading manufacturers are optimising profitability with data-driven cost calculation techniques.
Transform your costing strategy
Discover our software solutions to see for yourself. We're happy to design an individualized package for your business upon request.