Die Rolle der Produktkalkulation in der Fertigung
Eine präzise Produktkalkulation beeinflusst alle Unternehmensbereiche. Hier sind die wichtigsten Vorteile:
- Entwicklung neuer Produkte: Unterstützt Unternehmen dabei, Produkte vor Produktionsbeginn korrekt zu bepreisen und teure Überarbeitungen zu vermeiden.
- Lieferantenkosten-Benchmarking: Liefert Beschaffungsteams die notwendigen Daten, um Lieferantenpreise zu vergleichen und bessere Verhandlungen zu führen.
- Operative Effizienz: Identifiziert Engpässe und Ineffizienzen, wodurch Produktionsprozesse optimiert werden.
- Nachhaltigkeitsaspekte: Ermöglicht Unternehmen, ihren CO₂-Fußabdruck zu verfolgen und zu optimieren, ohne die Kostenkontrolle zu verlieren.
- Risikominimierung: Verhindert unerwartete Kostenüberschreitungen, die die Rentabilität gefährden könnten.
Wie man Produktkosten senkt: Best Practices
Kostenoptimierung bedeutet nicht, Abstriche bei der Qualität zu machen – es bedeutet, intelligenter zu arbeiten. Hier sind bewährte Strategien, die Hersteller anwenden, um Produktkosten zu senken, ohne Kompromisse bei der Qualität einzugehen:
Der Aufbau starker Beziehungen zu Lieferanten ist essenziell. Durch geschickte Verhandlungen und die Nutzung von Mengenrabatten können Hersteller bessere Konditionen für Rohstoffe sichern. Darüber hinaus hilft eine diversifizierte Lieferantenbasis, Risiken durch Unterbrechungen in der Lieferkette zu minimieren und eine konstante Materialverfügbarkeit zu wettbewerbsfähigen Preisen sicherzustellen.
Die Integration von Software zur Kalkulation von Fertigungskosten in die Produktionsprozesse minimiert manuelle Fehler und beschleunigt Abläufe. Automatisierung erhöht nicht nur die Genauigkeit, sondern entlastet auch die Belegschaft von repetitiven Aufgaben, sodass sich Mitarbeitende auf strategisch wertvollere Tätigkeiten konzentrieren können. Dies führt zu einer gesteigerten Gesamteffizienz.
Echtzeit-Kostenverfolgung implementieren
Der Einsatz von cloudbasierten Lösungen zur Echtzeitüberwachung von Produktionskosten ermöglicht sofortige Einblicke in die Kostenstruktur. Diese Transparenz erleichtert schnelle Entscheidungen und hilft, Budgetüberschreitungen frühzeitig zu erkennen und zu beheben, wodurch die Kostenkontrolle sichergestellt wird.
Die Anwendung von Design for Manufacturability (DFM)-Prinzipien stellt sicher, dass Produkte unter Berücksichtigung der Fertigungsprozesse entwickelt werden. Durch die Vereinfachung von Designs kann der Materialeinsatz reduziert und Montageprozesse optimiert werden, was zu erheblichen Kosteneinsparungen führt.
Die Durchführung von Should Cost Analysen ermöglicht die Schätzung der erwarteten Produktionskosten und hilft, Abweichungen in den Lieferantenpreisen zu identifizieren. Diese Methode gibt Herstellern eine stärkere Verhandlungsposition und offenbart potenzielle Einsparungen, die sonst unentdeckt bleiben könnten.
Koordination der Lieferkette verbessern
Eine enge Zusammenarbeit mit Lieferanten und Distributoren erleichtert eine präzisere Bedarfsprognose und ein effizienteres Bestandsmanagement. Eine bessere Koordination kann Skaleneffekte ermöglichen, Transportkosten senken und die Gesamtleistung der Lieferkette verbessern.
Die Umsetzung dieser Best Practices steigert sowohl die Rentabilität als auch die betriebliche Effizienz und verschafft Herstellern einen klaren Wettbewerbsvorteil.
Software vs. Excel für die Produktkalkulation: Warum digitale Lösungen überlegen sind
Viele Hersteller verlassen sich weiterhin auf Excel für die Kostenanalyse, doch Tabellenkalkulationen stoßen an ihre Grenzen und sind für die modernen Anforderungen der Produktkalkulation ineffizient. Nachfolgend ein Vergleich zwischen Excel und spezialisierter Software für das Produktkostenmanagement:
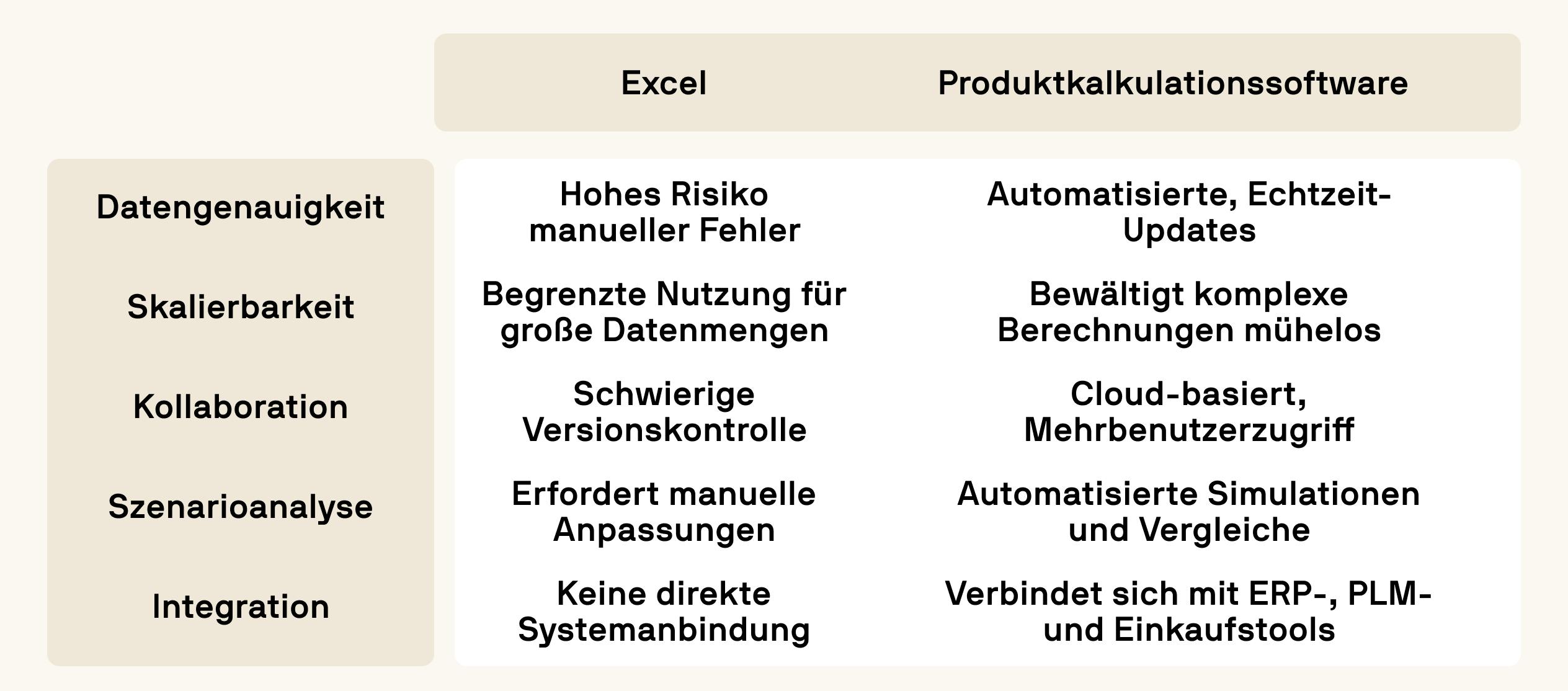
Manuelle Dateneingabe führt zu Fehlern, große Datenmengen verlangsamen die Leistung und die Zusammenarbeit wird durch Versionskontrollprobleme erschwert. Szenarioanalysen erfordern mühsame manuelle Anpassungen, und ohne direkte Integration mit ERP- oder PLM-Systemen stören Datenübertragungen den Workflow.
Diese Herausforderungen werden mit einer spezialisierten Lösung behoben. Automatische Updates verbessern die Genauigkeit, leistungsfähige Rechenkapazitäten verarbeiten große Datenmengen nahtlos, und cloudbasierter Zugriff ermöglicht eine Echtzeit-Zusammenarbeit. Eingebaute Szenario-Simulationen liefern schnelle Kostenvorhersagen, während nahtlose ERP- und PLM-Integrationen die Prozesse optimieren.
Der Wechsel zu einer Kostenoptimierungssoftware spart nicht nur Zeit, sondern erhöht auch die Transparenz über Kostenstrukturen, verbessert die Rentabilität und unterstützt fundiertere Entscheidungen.