The Role of Product Costing in Manufacturing
Accurate product costing impacts every part of a business. Here’s how:
- New Product Development: Helps companies price products correctly before production starts, reducing costly revisions.
- Supplier Cost Benchmarking: Gives procurement teams the data they need to compare supplier pricing and negotiate effectively.
- Operational Efficiency: Identifies bottlenecks and inefficiencies, leading to more streamlined production.
- Sustainability Considerations: Enables companies to track and optimize their carbon footprint while staying cost-efficient.
- Risk Mitigation: Prevents unexpected cost overruns that can threaten profitability.
How to Reduce Product Costs: Best Practices
Optimizing costs doesn’t mean cutting corners - it means working smarter. Here are proven strategies manufacturers use to reduce product costs without sacrificing quality:
Optimize Material Sourcing
Building strong relationships with suppliers is fundamental. By negotiating favorable terms and exploring bulk purchasing options, manufacturers can secure better rates for raw materials. Additionally, diversifying the supplier base can mitigate risks associated with supply chain disruptions, ensuring consistent material availability at competitive prices.
Integrating manufacturing cost estimation software into operations minimizes manual errors and accelerates production processes. Automation not only enhances precision but also frees up human resources for more strategic tasks, leading to overall efficiency gains.
Implement Real-Time Cost Tracking
Utilizing cloud-based software for real-time monitoring provides immediate insights into production expenses. This transparency enables swift decision-making and the ability to address cost overruns promptly, maintaining budgetary control.
Applying Design for Manufacturability (DFM) principles ensures products are designed with manufacturing capabilities in mind. Simplifying designs can reduce material usage and streamline assembly processes, leading to substantial cost savings.
Conducting should cost analyses involves estimating the expected costs of production to identify discrepancies in supplier pricing. This practice empowers manufacturers to negotiate more effectively and uncover potential savings.
Enhance Supply Chain Coordination
Collaborating closely with suppliers and distributors fosters better demand forecasting and inventory management. Such coordination can lead to economies of scale, reduced transportation costs, and improved overall supply chain efficiency.
Implementing these best practices improves profitability and operational efficiency, giving manufacturers a competitive edge.
Software vs. Excel for Product Costing: Why Digital Wins
Many manufacturers still rely on Excel for cost analysis, but spreadsheets come with limitations that make them inefficient for modern product costing needs. Below is a comparison of Excel versus specialized product cost management software:
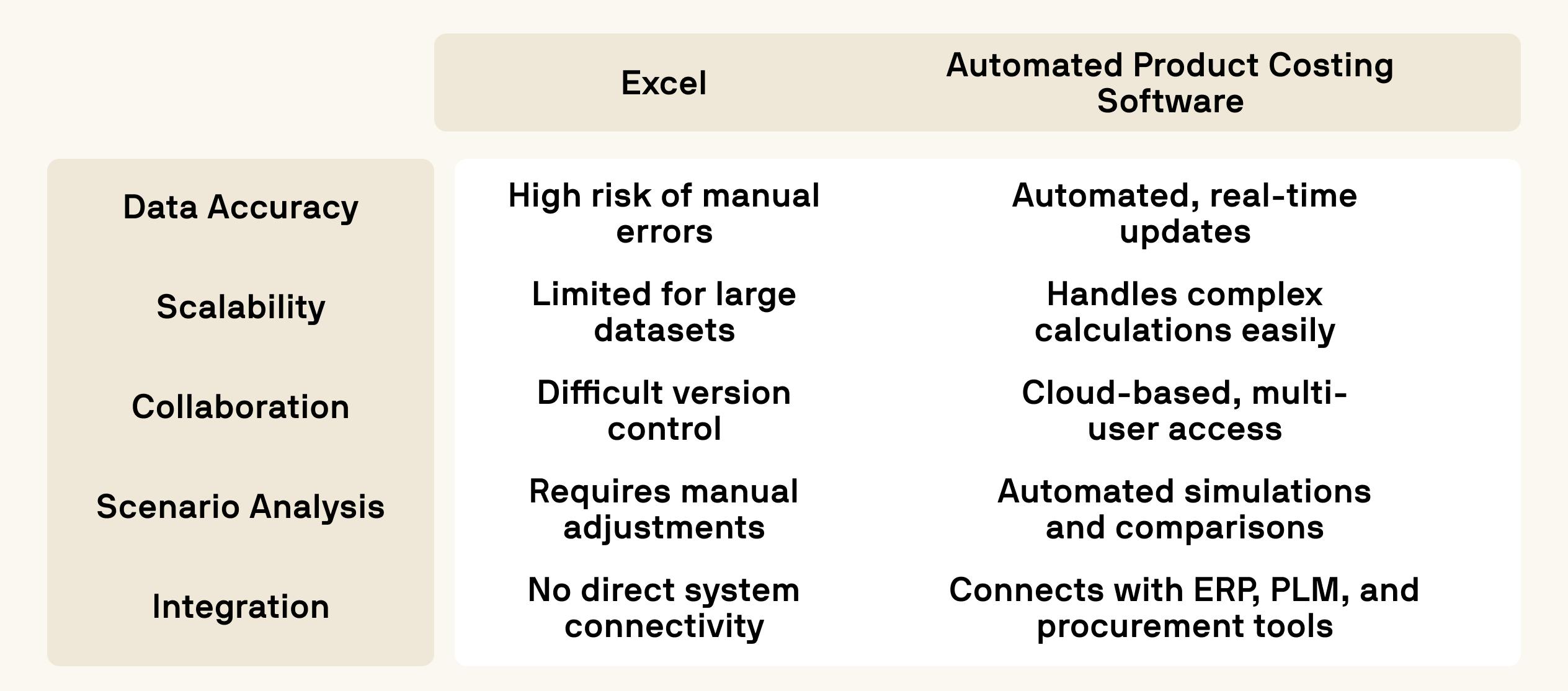
Manual data entry leads to errors, large datasets slow performance, and collaboration becomes messy with version control issues. Scenario analysis requires tedious manual adjustments, and without direct integration with ERP or PLM systems, data transfers disrupt workflows.
Product costing software solves these challenges. Automated updates improve accuracy, advanced computing handles large datasets seamlessly, and cloud-based access ensures real-time collaboration. Built-in scenario simulations enable fast cost predictions, while seamless ERP and PLM integrations streamline operations.
Switching to a cost optimization software not only saves time but also provides greater cost visibility, enhancing profitability and decision-making.