If You Involve Cost Engineering Too Late in the Design Phase, You’re Wasting Money
Imagine being asked to reduce the cost of a product after it has already been designed, sourced, and approved. Now you need to make changes without delaying the timeline or compromising quality. For many cost engineers, this situation is sandly quite common.
The main issue is timing. A Harvard Business Review article indicates that up to 80% of a product’s cost is determined by the time the design is finalized. This statistic emphasizes where companies should focus their efforts. Unfortunately, cost engineers are often brought into the process too late, when most cost-saving opportunities are no longer available.
This reactive approach rarely results in significant savings. Instead, it wastes time, budget, and team energy. A better solution is to move cost analysis upstream, leveraging product costing software that allows for fast and reliable early-stage evaluations. By addressing cost concerns during the design phase, companies can create a more efficient and cost-effective product development process.
Establishing a product’s design calls for crucial choices—about materials made or bought, about how parts will be assembled. When senior managers put most of their efforts into analyzing current production rather than product design, they are monitoring what accounts for only about a third of total manufacturing costs—the window dressing, not the window.
What Happens When Cost Decisions Come After Design Freeze
Once a design is frozen, most cost decisions have already been made: geometry, materials, manufacturing processes, and supplier quotes are all locked in. Requesting cost reductions at this point can only happen through costly changes.
A study on engineering change costs found that late-stage design modifications can be 5 to 100 times more expensive than those made during early development. A simple design adjustment - like adding a structural rib - may cost only €500 in CAD time during concept phase. The same change after tooling could cost €50,000 and delay start-of-production by weeks.
This way of working drains resources and frustrates teams. It also reinforces the perception of cost engineers as “fixers”, rather than as strategic contributors to product development.
By influencing design decisions early - including material choice, part geometry, and manufacturing routes - companies can reduce costs, simplify assembly, and improve sustainability outcomes. All without last-minute compromises.
Tset supports this shift by providing tools that make design-to-cost analysis possible during active development discussions.
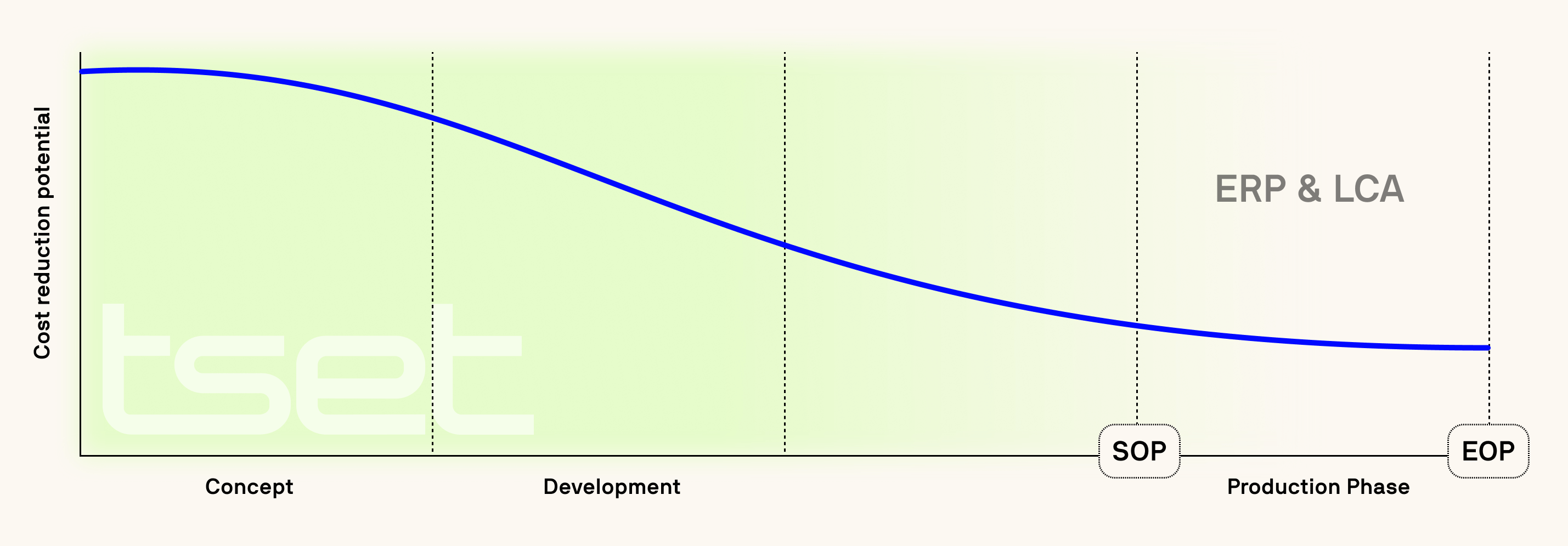
The High Cost of Missed Timing: Why Early Input Matters
Industry studies and experience show that late-stage cost-downs are typically 30–50% less effective than early-phase optimizations. The limited flexibility after design freeze means cost engineers can only trim around the edges, rather than influence the core drivers. According to Deloitte’s study on cost transparency, early visibility into cost structures allows teams to identify improvement opportunities when changes are less costly and more impactful.
The reason is simple. As the project progresses, the available options become more limited. By this stage, the product has already been defined, and making changes may lead to delays, increased tooling costs, or potential quality issues. In contrast, considering costs early in the process allows for more flexibility. Adjustments can be made quickly and with less friction. This approach empowers teams to make informed trade-offs instead of making reactive cuts.
Tset's product costing software is specifically designed to support this type of early, iterative analysis, thereby enabling both design and procurement teams to test, compare, and simulate options well before the design freeze.
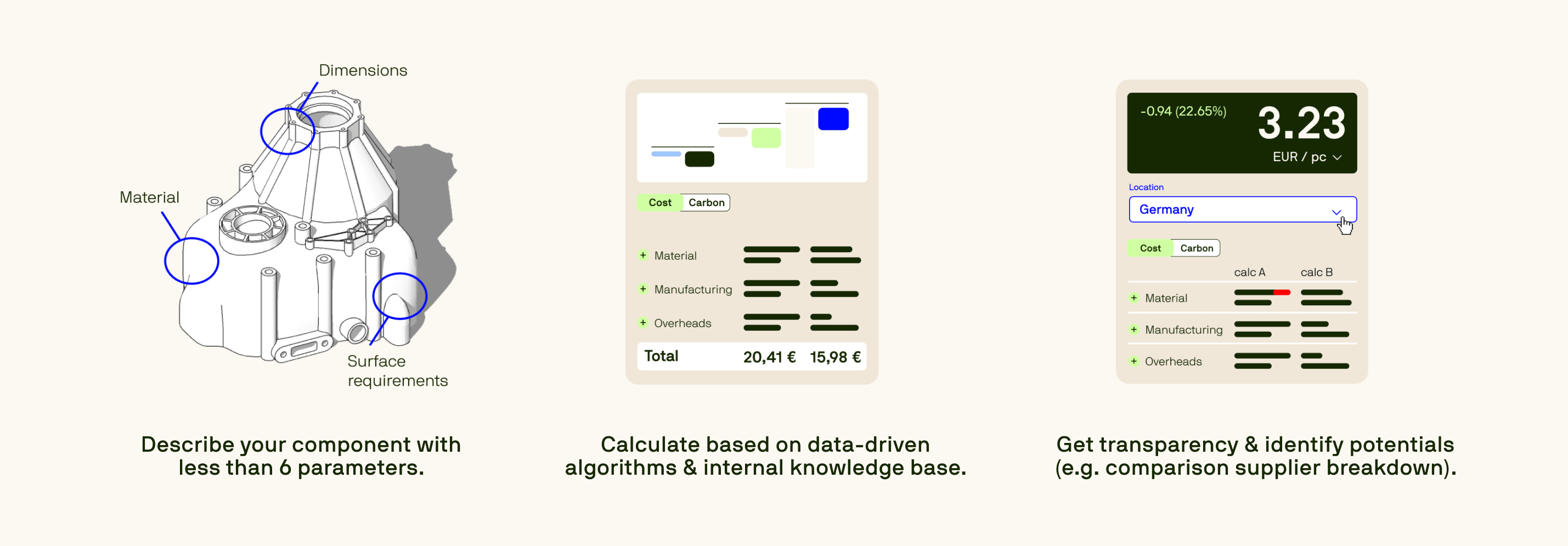
Bringing Cost Engineering into the Design Phase - Faster, Easier, Smarter
If the benefits of involving cost engineers early are so clear, why are they often brought in late? There are three main barriers:
-
Lack of accessible data
-
Inefficient tools, such as Excel
-
The perception that early-stage cost estimates are too complex or inaccurate
Early-stage cost estimation often suffers from missing data, limited tool support, and high manual effort. This discourages teams from engaging cost experts until the design is more stable.
Tset’s cost engineering software removes the typical roadblocks to early-stage cost engineering by providing a modern, automated, and flexible solution:
-
Get full bottom-up cost calculations in seconds, powered by automated costing modules and a central knowledge base.
-
Simulate multiple design variants using early 3D models, shapes, or part families to compare material, process, and geometry choices - even without a complete BOM.
-
Evaluate cost impacts directly during design reviews, enabling fast decision-making across engineering and procurement.
-
Collaborate across teams in a centralized, cloud-based software, with consistent costing logic and automatic version control.
-
Onboard users quickly with an intuitive interface and role-based access, thereby enabling even semi-experts to contribute confidently to cost discussions.
-
Simulate scenarios in real-time to support faster trade-off decisions and avoid late-stage surprises.
By replacing slow and fragmented processes with a purpose-built automated costing tool, Tset enables teams to act more quickly and confidently.
Achieve 30% cost reduction with early-stage product optimization
Read our new case study to learn how the implementation of Tset in the crucial product concept phase maximized cost efficiency while maintaining all product requirements.
Rethinking Cost Engineering: From Reactive to Proactive
As timelines shrink and manufacturing grows more complex, early cost input is critical. Today’s cost engineers are strategic partners who guide design, sourcing and sustainability choices. As Harvard Business Review puts it, “Design is a strategic activity, whether by intention or by default.” Tset supports this shift by giving cost teams the tools to influence product costing decisions early - working alongside R&D and procurement to build smarter, leaner, and more sustainable products.
Stop Firefighting Costs. Start Influencing Them.
By applying product costing software early in the development cycle, manufacturers unlock savings, speed up launches, and align with CO₂ goals. Book a demo to see how Tset supports early design costing and better decisions.
1. What is design-to-cost in product development?
Design-to-cost (DTC) is a cost management approach that treats cost as a design constraint from the start of product development. It ensures that decisions about materials, geometry, and manufacturing processes are made with cost impact in mind. This helps teams meet target pricing without compromising on quality or performance.
Key benefits of design-to-cost:
- Reduces expensive late-stage changes
- Supports cross-functional collaboration
- Aligns cost with sustainability goals
- Enables early trade-off decisions using costing tools like Tset
2. Why is product cost analysis more effective early in the design phase?
Product cost analysis is most effective before design freeze because 70–80% of product costs are locked in during the design phase. After that, changes become costly and disruptive. Early analysis allows teams to shape core cost drivers instead of reacting later.
3. What happens if cost engineering is done too late?
Late-stage cost engineering limits options and increases costs. Studies show that changes after design freeze can be 5–100x more expensive than if made earlier. This often causes delays, quality risks, and missed CO₂ targets.
Risks of late involvement:
- Expensive engineering changes
- Tooling delays
- Inefficient sourcing
- Reactive cost cuts instead of strategic design
4. How does product costing software improve early-stage decisions?
Product costing software automates and accelerates early cost analysis. It allows teams to estimate and compare costs using early 3D models and part data - before finalizing the design.
With product costing tools like Tset, teams can:
- Run real-time cost simulations
- Compare materials and processes
- Collaborate across departments
- Generate cost breakdowns in seconds
5. What is the difference between reactive and proactive cost optimization?
Reactive cost optimization occurs after the design freeze and offers limited savings with higher risk. Proactive optimization happens early in development, allowing teams to influence design choices, reduce cost more effectively and avoid delays. With cost engineering tools like Tset, proactive strategies lead to smarter decisions and better outcomes.