Why Job Cuts Are Surging in the Automotive Supply Chain
The automotive sector is undergoing structural change, and suppliers are under pressure from multiple directions. These are the key factors driving the current wave of job losses:
1. Inflation and Cost Pressure
Energy, labor, and raw material costs continue to rise. According to a KPMG report, supply chain disruptions have significantly contributed to inflationary pressures, affecting both demand and supply. These rising costs are squeezing supplier margins, making it increasingly difficult to maintain profitability without resorting to cost-cutting measures.
2. EV Growth Not Filling the Gap
Despite widespread headlines, EV sales are slowing in Europe. In Germany, for example, registrations dropped by 27 % in 2024. This decline means the EV boom has not been sufficient to absorb the jobs lost on the combustion side. While the EV transition remains essential to long-term sustainability goals, it comes with disruption. The International Monetary Fund warns that the shift will have “far-reaching” effects on investment, production, and employment, thereby illustrating how complex and challenging this moment is for suppliers.
3. OEMs Pushing for Lower Prices
Original Equipment Manufacturers (OEMs) are asking suppliers to absorb these rising costs while still reducing prices. With margins under pressure, many suppliers respond by cutting headcount. For example, automotive logistics providers are experiencing increasing cost pressures as OEMs push for savings to sustain EV investment and stay competitive.
4. Lower Demand for Combustion Engine Components
As the industry pivots to electric vehicles (EVs), demand for traditional combustion engine parts is falling. Global sales of internal combustion engine vehicles peaked in 2017 and have steadily declined since, according to data from Our World in Data. This trend reflects a broader shift in both consumer behavior and manufacturing priorities. Many Tier-2 and Tier-3 suppliers have long specialized in components that are now becoming obsolete at scale.
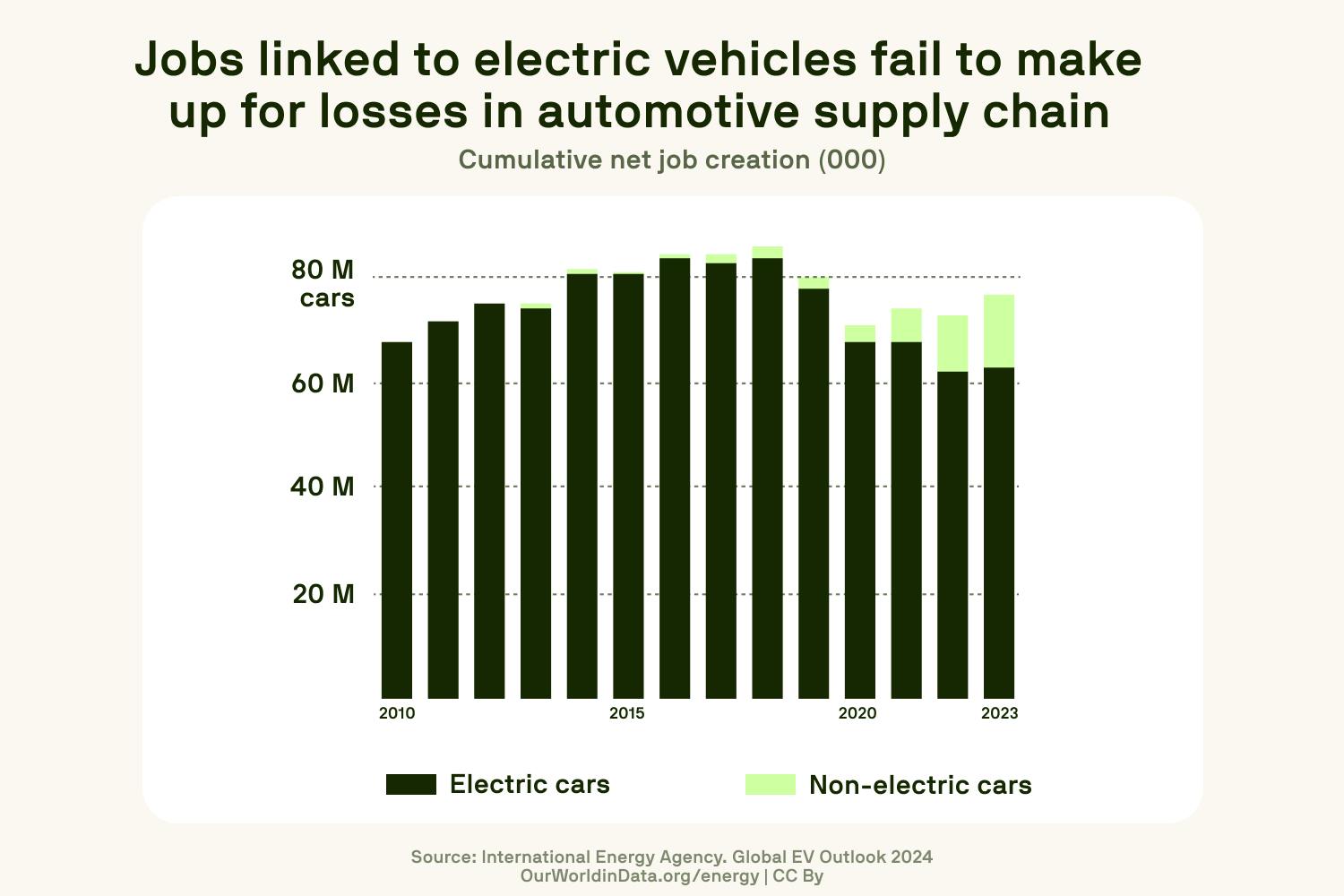
The Missing Link: Cost Optimization in Crisis Prevention
Cost engineering is about analyzing, managing, and improving product costs throughout the lifecycle. However, in many supplier organizations, the function is either missing or underdeveloped. Instead of using structured data and consistent calculations, teams often rely on disconnected spreadsheets and outdated tools. This leads to:
- Different costing practices across teams
- A lack of clarity on true cost drivers
- Slow response times when evaluating cost-saving options
When profits shrink and visibility is low, job cuts often become the default response.
Structured product cost management provides an alternative. By improving visibility and enabling faster, data-driven decisions, it gives companies the tools to navigate volatility without defaulting to reactive cost-cutting measures.